
Audits and Verifications
As an independent third-party we provide verifications, inspections and audits in accordance with the applicable regulations for the actual unit.
We emphasize that the management system and procedures are designed to fit the purpose and that the organization complies with this, further we evaluate the technical integrity of equipments and systems. The interaction between human, organizational and technical barriers are all factors which form the basis for our the reviews. Ensuring safe and efficient operation and within required standards, criteria and legislation.
We have gained a reputation for delivering value through:
-
Safety improvement; by early detection and prevention of safety hazards
-
Cost reduction; by pinpointing areas of concern at an early stage and by visualising solutions to comply with rules, regulations and contract
-
Providing priorities for the organisation early in the project lifecycle
-
Well prepared and optimized acceptance testing, based on historical data and competent personnel
-
Provision of early visibility and confidence for stakeholders
-
Online reporting, by providing documentation and continuous follow-up
Take a look at our customers and reference list here.
Why?
Our independent audits and verifications will help your company to identify, monitor and follow up potential safety risks and deviations. A set of "new eyes" might be able to pinpoint areas of improvement that normally would go under the radar by the use of internal resources.
VTC Offshore has a well proven methodology for conducting our audits and verifications where we emphasize the interaction between technical integrity, organisation and human factors.
By performing risk based audits, it will increase your possibility to receive an early warning of decreasing performance, and let you take the required actions before and incident occurs.We use PAR-Management™ to trend the results and follow up safety performance over time.
We have extensive knowledge of Maintenance systems and Maintenance Management and the Rules and Regulation governing NSC for Maintenance
VTC Offshore personnel have long experience with Maintenance Management. We have the necessary knowledge to perform or assist with all aspects of maintenance management. The following list gives an overview over some of the areas we cover.
-
Failure Mode, Effect and Criticality Analysis (FMECA)
-
Reliability Centred Maintenance (RCM)
-
Performance Standards and Barrier Management
-
Maintenance Management Procedures
-
Maintenance System Improvements
-
Key Performance Indicators (KPI)
-
Maintenance Effectiveness
-
Spare part Analysis
-
Continuous Class programs
-
Condition Based Maintenance (CBM)
Maintenance Audits
The maintenance audit will focus on the rig owner’s responsibility to establish, document, implement and maintain a system for maintenance of his facilities and equipment. Subsequently, the audit will assess, verify and report the actual situation of the implementation of the maintenance system.
Furthermore, the maintenance audit will confirm the rig owner’s ability to continuously improve the maintenance system’s efficiency and to pro-actively utilize inspection results, the wear & tear measurements, operations time (age, conditions and any relevant analysis) for further developing of the preventative maintenance program.
Some typical maintenance audit approaches will be:
- is the process’ identified and appropriately described?
- are responsibilities assigned?
- are the procedures implemented and maintained?
- is the improvement process’ effective?

Well Control
Well control system and equipment in particularly the Blowout Preventer is a critical component for safety. The BOP is an assembly of integrated and interdependent systems. Well control equipment and systems, are designed to withstand extreme pressures, preventing catastrophic blowouts from occurring during drilling.
Relevant areas VTC Offshore can help you with;
-
Verify that BOP has been tested for cutting of relevant drill string components.
-
Verify that the system is maintained according to relevant requirements with regard to valves, piping, thickness measurement, thickness measurement, pressure and temperature gauges and pressure testing.
-
Accumulator volumetric capacity, pressure requirements and BOP response time.
-
Review system ability to record corrective maintenance jobs/failed tests to be used for continuous improvement.
-
Spot check routine and frequency of leak testing of drilling BOP
-
Verify available certificates and inspection reports for relevant components.
-
BOP Control panels.
-
Choke operation and remote control system
-
Burner boom system
-
Facilities for glycol injection.
-
Emergency training/ drills for relevant drilling personnel e.g.
-
Kick drills
-
Pit drills
-
Choke drills
-
Training for emergency line up from pump room to cement unit
-

Management System
A good quality management system is an investment for your company.
This provides a basis for systematic improvement and management of the various business processes, helping to ensure customer satisfaction.
We assist your company with the expertise and resources required to reach compliance with ISO 9001.
By using PAR-Management™, we ensure an effective implementation, review and follow-up.
The main objective of quality management is to ensure that:
-
Corporate policies and principles is an integral part in all activities
-
The company conducts activities in accordance with internal and external requirements, standards and regulations
-
The company provides products and services that are characterized by high quality
-
The company follows up suppliers and partners to ensure that the requirements and guidelines are safeguarded
-
Ensures continuous improvement, learning and development
-
Competitive advantage by being a preferred supplier
-
An ISO 9001: 2008/ 2015 compliant company should have an effective system for improvement and development.

Safety Systems
The oil and gas industry are facing more complex systems within ICT and automated solutions. Technological development and integrated solutions require clear policies in order to operate and maintain the system without compromising the safety level. The increasing interconnection between safety and control systems may affect the independency of each system. VTC Offshore has performed several inspections related to SIS (safety integrated system), and we have experienced that many of the issues connected to this needs to be highlighted.
Fire & Gas System
Fire and gas systems onboard offshore installations is one of the main barriers to prevent a potential major accident. Unfortunately, our surveyors has identified a number of serious errors and omissions related to F&G systems. The importance of the technical integrity and compliance with procedures is something we take very seriously. We find that both our customers and the auditee appreciate the value of a thorough review of these systems.
A verification of the fire and gas system can typically include review of:
-
Hazardous area classification
-
Cause and Effect diagrams
-
Power supply and redundancy
-
Detector coverage
-
Operational Procedures
-
Training and competence
-
Installation
-
F&G Philosophy
In addition, we also perform functional testing to verify that selected effects are according to design and philosophy.
Emergency shutdown system
Activation of the ESD system will ensure the safest possible condition for the Installation and the equipment to minimise the consequences of an emergency related to uncontrolled releases of hydrocarbons or an outbreak of fire. The ESD System is used to provide a safe and rapid shutdown of systems and equipment. The ESD System processes input signals from manual pushbuttons and selected F&G signals.
The list below highlight other issues related to a typical VTC inspection:
-
ESD Philosophy review
-
Adherence of procedures
-
Ignition source control and interface to F&G system
-
Cause and effect diagrams
-
Power supply and redundancy
-
Operational Procedures
-
Training and competence
-
Installation

Electrical Systems
Comprehensive regulatory requirements and complexity of electrical systems have in many cases led to budget overruns for new buildings and extensive modifications to units in operation. Work processes, electrical equipment/ systems integrity and methods of working are important to prevent incidents and injuries.
We contribute with our expertise as appropriate in the execution of verifications of management systems, policies, design, implementation of standards, codes and the adoption of good practice are important aspect of our inspections.
We use historical data and experience from safety case assessment, investigations and verification reports as inputs to prioritising inspections.
-
Safe use and work on/nearby electrical installations
-
Installation
-
Power Management Systems
-
Ex-equipment and ignition source control
-
Procedures/ lessons learned/ Best Practice
-
Documentation/ philosophies/ manuals
-
Maintenance of electrical equipment
-
Roles and Responsibilities
-
Training and competence
Drilling Control System
By using multidiscipline surveyors, we are able to verify the operational conditions towards technical limitations.
The verification will aim to identify the functionality and safety integrity within DCS and its interfaces.
-
Training and competence
-
User interface / HMI (Human Machine Interface)
-
Online support
-
Handling of software - changes and versions
-
Operational and technical procedures
-
Anti-collision
-
Maintenance
-
Interfaces
-
Alarm philosophy
-
Installation
-
Ex-certification of relevant equipment
VTC Offshore focus on sharing valuable learning, knowledge and experience across organizations and companies.
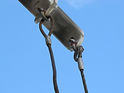
Lifting equipment - Lifting operations - Material handling
The objective of the verification activity is to evaluate drilling contractor's management and control with regards to materials handling. The technical condition of lifting equipment and the performance of the lifting operations are also assessed in relation to relevant regulatory requirements.
The goal is to verify drilling contractors established improvement activities within lifting equipment and operations, with primary focus on the drilling area.
Survey within drilling area according to NORSOK, R-003N and Norwegian Oil and Gas Association guidelines 081 (Former OLF 081).
-
Safe use of lifting equipment
-
Management
-
Risk assessment
-
Training and competence
-
Planning
-
Limitations
-
User check

Major Accident
Considerable effort has been put into learning from the Deepwater Horizon (DwH) accident.
The overall goal for a verification of the barriers against major accidents is to ensure and document that systems are designed and built to fulfil its purpose. Lessons learned and risk awareness are important aspects in our verifications . Following up the operators and the drilling contractors and their responsibility in the operational phase – and how they understand and exercise this responsibility.
In recent years, incidents on the Norwegian shelf and at the land facilities have also had the potential to become major accidents. The incident on Snorre A (2004) is only one example of a potential major accident, where in total 28 barrier breaches were identified. Incidents on Gullfaks and Statfjord confirm that this can happen, and that we must strive to safeguard implementation of the "lessons learned".
The last major accident on a facility on NCS took place in 1986, in connection with the shallow gas blowout on the mobile facility West Vanguard.
Mapping of major accident risk:
Experiences from audits, reporting of accidents and near misses, investigation of major incidents and R&D activities are important sources.
As regards the development of major accident risk, the results from the "Trends in risk level" are crucial. Specific areas where the probability of major accidents is the greatest have been identified through this mapping:
-
Hydrocarbon leaks
-
Serious well incidents
-
Damage to load-bearing structures and maritime systems
-
Ships on collision course
There is a multitude of technical, operational and organisational factors within these areas, and each factor can, alone or in combination, cause accident incidents or affect a possible course of events.
A major accident will, in addition to the human aspects, also have substantial consequences for society at large and the reduction of major accident risk is therefore a crucial reason for the formulation of existing health, safety and environment regulations.
For those affected by an accident, the loss will be far greater than what appears in the socio-economic evaluation – the value of a life cannot be expressed in money.
"Source PSAN"

Environment
Verifications of systems related to environmental protection and containment.
Review of relevant barriers established and other relevant areas e.g.;
Management focus and involvement
Policy and strategy
HSE involvement / training
Management systems and procedures
zero discharge – philosophy
non-conformance history / close out of previous incidents
experience transfer
Drainage Systems
open and closed drain, «contained rig"
single / double barriers
Contingency
Report routines, acute discharges
Use of chemicals and drilling fluids
Chemicals storing
Use of chemical
Hose Stations – maintenance
Couplings, Valves, Hoses
Slip joint – maintenance
Fail safe system, PM program, Certificates, Spare parts
Slope/ Cuttings System
Handling of slope, Slope classification, Transport / Handling of skips, Manifestation / Reporting
Bulk transfer system
Hoses, piping,
Emergency Transferring
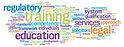
Training and Competence
Training and competence have always had a strong focus by the authorities considering that this field has had challenges in safety, working environment and human / machine interaction, and that the risk of serious accidents is present.
Personnel working on the Norwegian Continental Shelf shall at all times have the competence as necessary to carry out activities in a safe manner in accordance with environmental, health and safety legislation.
VTC has on several occasions carried out verifications and helped its customers to ensure that their suppliers have the training and competencies required.
Our checklists defines what is required of theoretical and practical of knowledge, for the use of systems and equipment according to the use for each position, and/ or the necessary skills.

Health
VTC Offshore can assist your company with the expertise and resources required to reach compliance with rules, regulations and standards for health and hygiene.
-
Development of management system for health services.
-
Verifications and reviews of health, hygiene and potable water related issues
-
Design and layout of hospital facilities
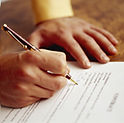
Contract
The importance of a “good contract”:
VTC Offshore personnel have more than 30 years of experience with contracts in the oil and gas industry.
The importance of implementing years of experience and historical data as a basis for making the best contract possible, will have substantial benefits for the organization, i.e.:
-
Less risk for cost overrun (reduced cost)
-
No delays
-
Less time spent for contractual discussions/negotiations
-
No variation orders
-
No risk for bad reputation
-
No risk potential for law suits
-
Better safety
-
Better quality
Our specialties are rig contracts and other contracts related to drilling operations.
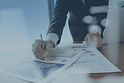
Projects
As a qualified independent third-party, VTC Offshore can help you being foresighted and significantly improve your possibilities for project success (quality, cost and time of delivery).
-
Meet site-specific requirements, safety standards and local regulations
-
Minimize risks through site-specific assessment of your project and independent inspection and testing of your critical components
You will improve your possibility to meet budget and schedule, and enable you to detect design deviations at an early stage.
Our project verification services include:
-
Verification for all project phases
-
Fabrication inspection and witnessing
-
Factory Acceptance Tests (FAT)
-
Pre-audits / audits
-
End-of-warranty inspection
-
Verification of design
-
Commissioning supervision
-
Verification of electrical systems and design

Loose Drilling Equipment
The objective of the verification activity is to evaluate the drilling contractor’s management and control concerning maintenance and follow-up of loose drilling equipment.
The technical condition of loose drilling equipment is also assessed in relation to relevant regulatory requirements.
Dropped Objects
Dropped objects have historically been a hazard on drilling rigs. The oil and gas industry and the governments has put a high focus at this area. VTC has performed audits regarding DROPS with the aim to contribute to a safe working environment
During our audits, we focus on the highlighted bullet points below:
-
Verify that procedures are implemented and followed
-
Verify that tools used at height are properly secured in all areas.
-
Verify that Dropped Objects are addressed in all planning sessions
-
Monitoring of the task with specific focus on Dropped Objects.
-
Follow-up of safety alerts related to Dropped Object.
-
Access control to dropped object zone (e.g. red zone).
-
Dropped objects

